汽车电气化竞争的历程
多年来,汽车制造商面临着对更大功率需求的挑战。早期,汽车使用6V电池供电,直到大约1950年,汽车系统发展成为12V电源,以满足更大功率的永久需求。汽车制造商不仅需要预测窗户、转向系统和座椅的新供电需求,还需要更多的电源来满足新的高压发动机。
近来,在CO2排放合规性的刺激下,OEM厂商不得不重新考虑如何再次为汽车供电。尽管OEM厂商正在推出电动汽车,以达到这些标准,但目前还没有统一的方法来为电机和车辆的所有子系统供电。
电力需求的急剧增加使得这种不足更加明显。内燃机车的电源通常在600W到3kW之间。新的电气化电动车、混合动力车和插入式混合动力车(xEV)需要3kW到60kW以上的电力,比原来的电力高5-20倍。
5-20倍的增加会对车辆供电网络(PDN)的尺寸、重量和复杂性造成很大压力。这些需求会对能源效率、可靠性甚至舒适性和安全性产生负面影响,因为增加的尺寸和重量会导致车辆特性的妥协。如果汽车制造商继续使用传统的供电方式,就没有足够的空间来满足所有的电气需求。为了应对这个挑战,他们需要找到一个轻便紧凑的解决方案,这不仅可以缓解电源的明显增长,而且灵活,可以在整个产品线上重复使用。
除了主要的技术挑战,OEM厂商也在给自己增加压力,承诺在未来10年内实现产品的全面电气化,尽管如何实现这个目标的具体细节仍然是一个悬而未决的问题。在整个电动汽车市场,没有明确的方法来实现电气化的标准化。因此,尽管OEM制造商可能有相同的目标,但他们设计的PDN会有很大的不同。
多年来,电动汽车产量低于全球汽车总产量的1%。瑞士信贷全球汽车研究中心团队数据显示,这一比例将从2020年的11%飙升至2030年的62%,全球汽车销量将达到6300万辆。预计近一半(2900万)将完全电气化。
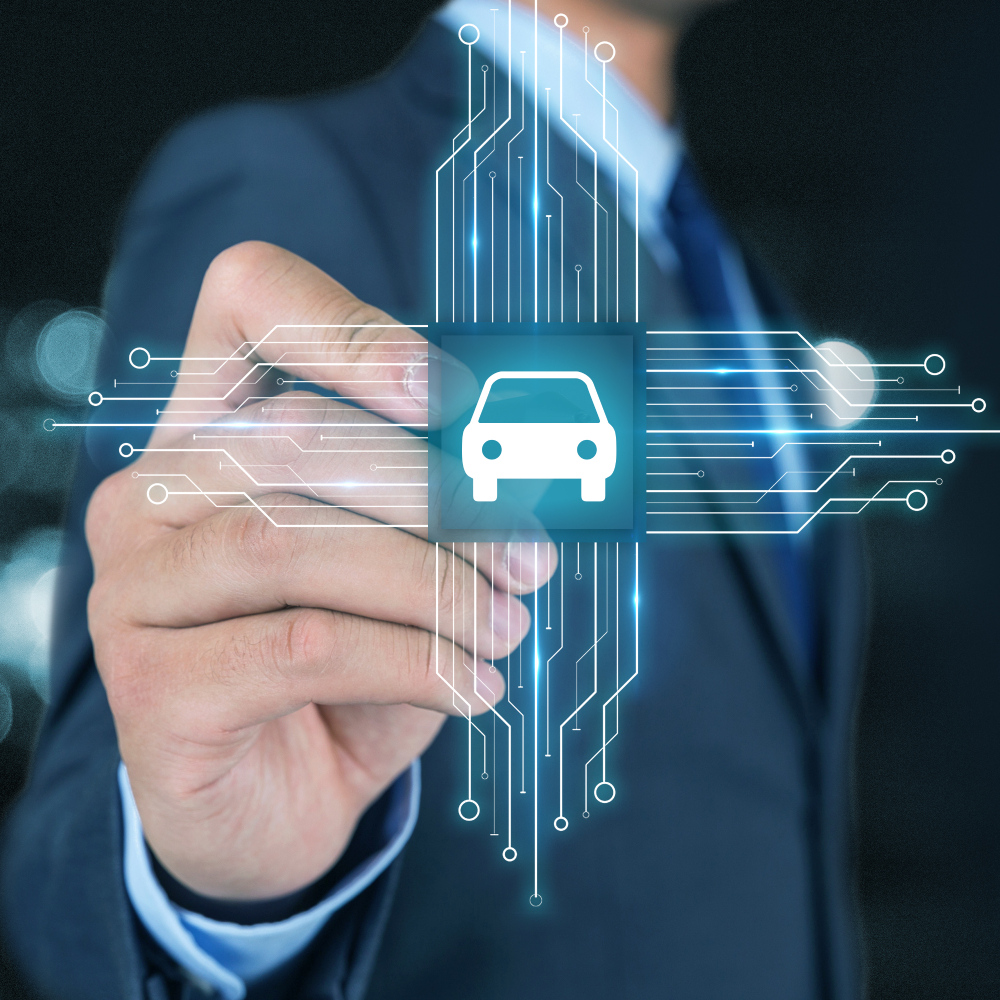
电动汽车爆炸式增长的推动因素又是什么?尽管排放达标和政府激励措施启动了这个过程,但正是消费者的欲望带来了这个巨大的需求,使得OEM厂商把电动汽车从细分市场推向了主流市场。如今,这些OEM制造商做出了大胆的承诺。
目前,OEM厂商正在为一些最受欢迎、最受欢迎的汽车实现电气化。普通悍马、福特新MachE(电动野马)和F150轻型旗舰卡车(闪电)正在实现电气化。由于它们具有令人兴奋的性能提升和时尚的设计,这些车型正在吸引大众的注意力。
这类新型汽车具有较好的快速充电技术和较低的维修费用,是刺激消费者需求,提高电动汽车利用率的催化剂。顾客看到了价值,所以增长势头越来越大。
汽车平台的数量、消费者选择、不同的动力系统结构、电池和充电配置的选择都增加了汽车电气化的复杂性,动力系统设计者必须解决。
为了优化汽车电气化,OEM厂商需要提高功率水平,缩小供电网络的尺寸和重量,提供更好的热管理和可重复使用性。设计电源系统的传统方法必须从复杂的定制分离设计转变为更小、更灵活、更容易使用、更高密度的模块化解决方案。
为了实现积极的电气化目标,OEM制造商必须重新考虑供电结构方案。除了找到有效的解决方案外,加速和优化电气化还必须满足三个要求。
功率密度:无论是设计快速跑车、轻型卡车还是家用车,OEM厂商都需要在有限的空间内提供尽可能多的电源。汽车需要紧凑高效的电源解决方案。
灵活性/可扩展性:许多车辆使用相同的平台,所以当修改共享相同平台的汽车、小型卡车和越野车的电源时,方便的电源扩展非常重要。
可重复使用性:为了实现整车电气化,OEM厂商需要在不同车型之间重复使用电源设计,加快上市进程。
(1)功率密度:
各种xEV平台使用的电源电子产品的尺寸和重量直接关系到车辆的性能、能源效率和电池的持续距离。为了跑得更远更快,OEM制造商积极缩小电源电子产品的尺寸和重量,鼓励开发团队降低车辆的重量。
一种效率为98%的小型母线转换器模块(BCM6135)重量仅为68克,可以轻松地与EMI滤波器、较小的散热结构和外壳相结合,取代25公斤的48V电池。它不但可以释放大量的空间和负荷,而且还可以节省125-250欧元的减重研发费用。在61×35×7毫米的小封装中,高密度电源模块将400~800V的主电池转换成48V,可以提供2kW以上的功率,功率密度超过4.3kW/in3(图3)
(2)灵活性/可扩展性:
为了节省时间、金钱和资源,OEM厂商设计者尽可能地将集成在车内的子系统标准化。但是,每一个子系统都会随着车内装饰的不同等级而有所不同。随着汽车电气化的发展,供电系统设计团队面临着供电需求不断变化的挑战。由Vicor提供的灵活、可扩展的模块化供电系统设计方法,允许设计者在各种动力系统(如SUV、厢式货车或轻型卡车)上实施标准化解决方案。
举例来说,一辆厢式货车的供电要求可能是5kW,但是对于一辆配有短排灯、拖具、犁具和交流发电机的轻型卡车来说,供电可能需要10kW。利用同样的平台和一点额外的空间,工程师可以迅速地在阵列中添加或移除通过预审的零件,以增加或减少功率。
此外,模块化设计还可以通过48V母线实现分布式电源架构,提供更高的灵活性。电源模块可以放置在便捷的位置进行局部48V/12V转换,可以放在储物箱后面,靠近储物箱,也可以放在每个车轮旁边。部署模块化解决方案不仅可以提供设计灵活性,还可以提供更好的方法优化电源变化和制造过程。
(3)可重复使用:
汽车车开发过程中,最常见的延迟之一是汽车使用的电子部件的审查。这个过程可能需要2~3年才能通过,为单个部件取得生产部件的认可程序。研究开发团队为了节约开发和审查时间,通常会想办法重复使用现有部件,节约宝贵的资源。
例如,基于分离式DC-DC转换器设计的传统PDN可能由200多个大型组件组成,但Vicor的先进技术只提供一个高密度电源模块。对于工程设计团队来说,为了实现相同的功能,认证一个模块比认证200多个独立组件节省了时间。
此外,Vicor模块化方法还允许工程师使用3-4种不同类型的可扩展部件模块,实现约300种供电组合。(图4)这种设计方法可以节省数百小时的时间和资源,可以帮助OEM制造商在电气化竞争中处于领先地位。
OEM厂商面临着巨大的挑战,不仅要跨越电气化的终点线,还要完成xEV系列的设计,带来长期的效益。采用模块化电源系统设计方法,可以在这一重要的市场份额竞争中提供竞争优势。现在需要以新的结构和拓扑的形式进行创新,不仅可以提供现在最高的性能,还可以在今后重复使用和配置。
传统的电源设计不能满足这种程度的灵活性和易用性。对于OEM厂商来说,为了达到积极的电气化目标,最好采用模块化方法,既能在多个重要层面提供最高性能,又能帮助他们满足最复杂的xEV电源需求。